Precision in Manufacturing: Prints, Calipers & Gauges
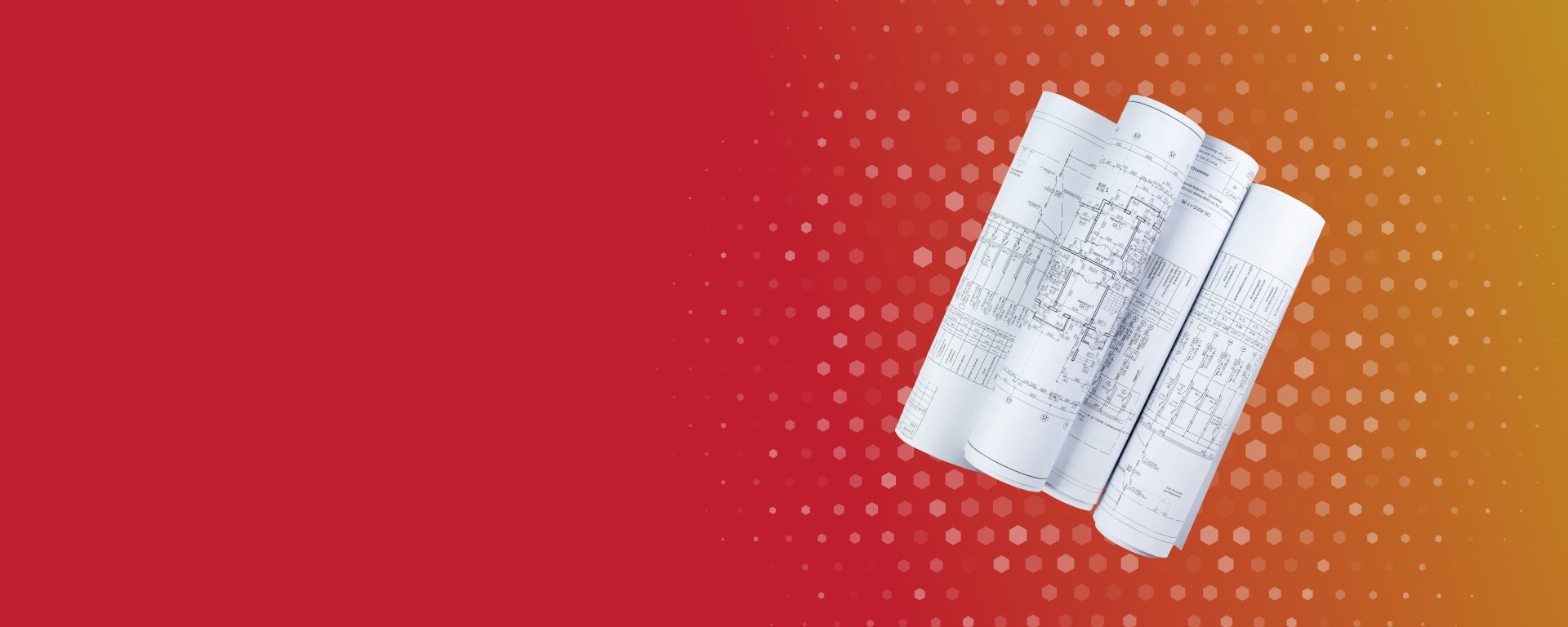
In the world of manufacturing, precision is everything. Whether you’re producing a simple bracket or a complex machined component, the ability to deliver parts that meet exact specifications is what separates high-quality manufacturers from the rest. Three critical pillars support this pursuit of precision: calipers, technical print comprehension, and thread gauges. Together, they ensure that parts meet design intent, function flawlessly, and exceed customer expectations.
Understanding Technical Prints: The Blueprint of Success
Technical prints are the foundation of any manufacturing process. They provide the detailed roadmap that guides production, outlining key specifications like dimensions, tolerances, materials, and finishes. Without the ability to read and interpret these prints, even the most advanced shop floor tools are rendered ineffective.
Key elements to focus on when reading technical prints include:
Print Revision: Always ensure you’re working with the most current version.
Tolerances: Understand the acceptable range of variation—this is crucial for quality control.
Section Views and Reference Dimensions: These provide deeper insights into hidden or critical features.
Common Symbols: Familiarity with diameter (⌀), depth (↧), and typical dimensions (TYP.) helps ensure you capture the complete picture.
Strong print comprehension enables teams to identify important details, anticipate potential challenges, and verify that every part aligns with the designer’s intent—saving time, reducing rework, and boosting customer satisfaction.
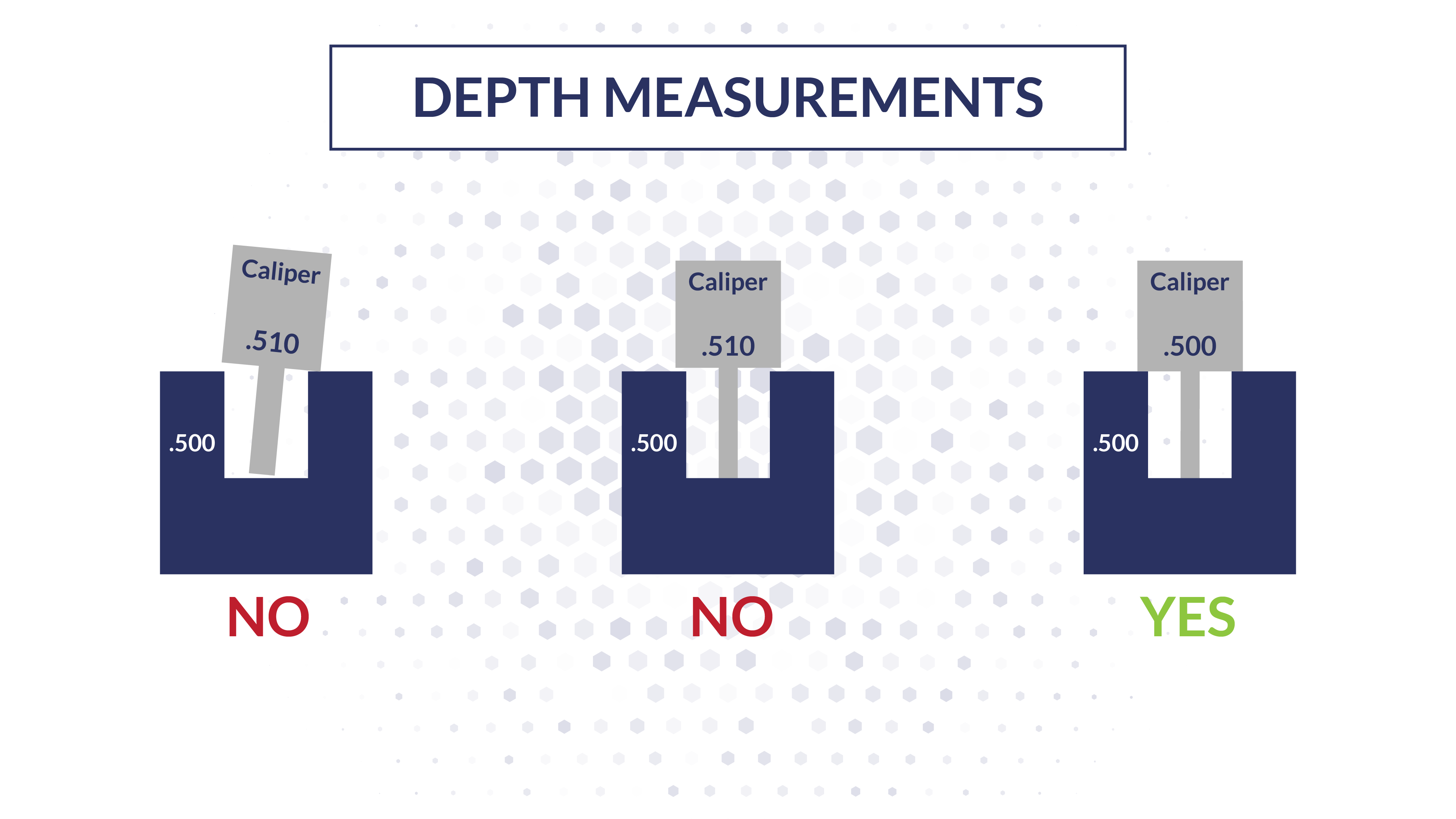
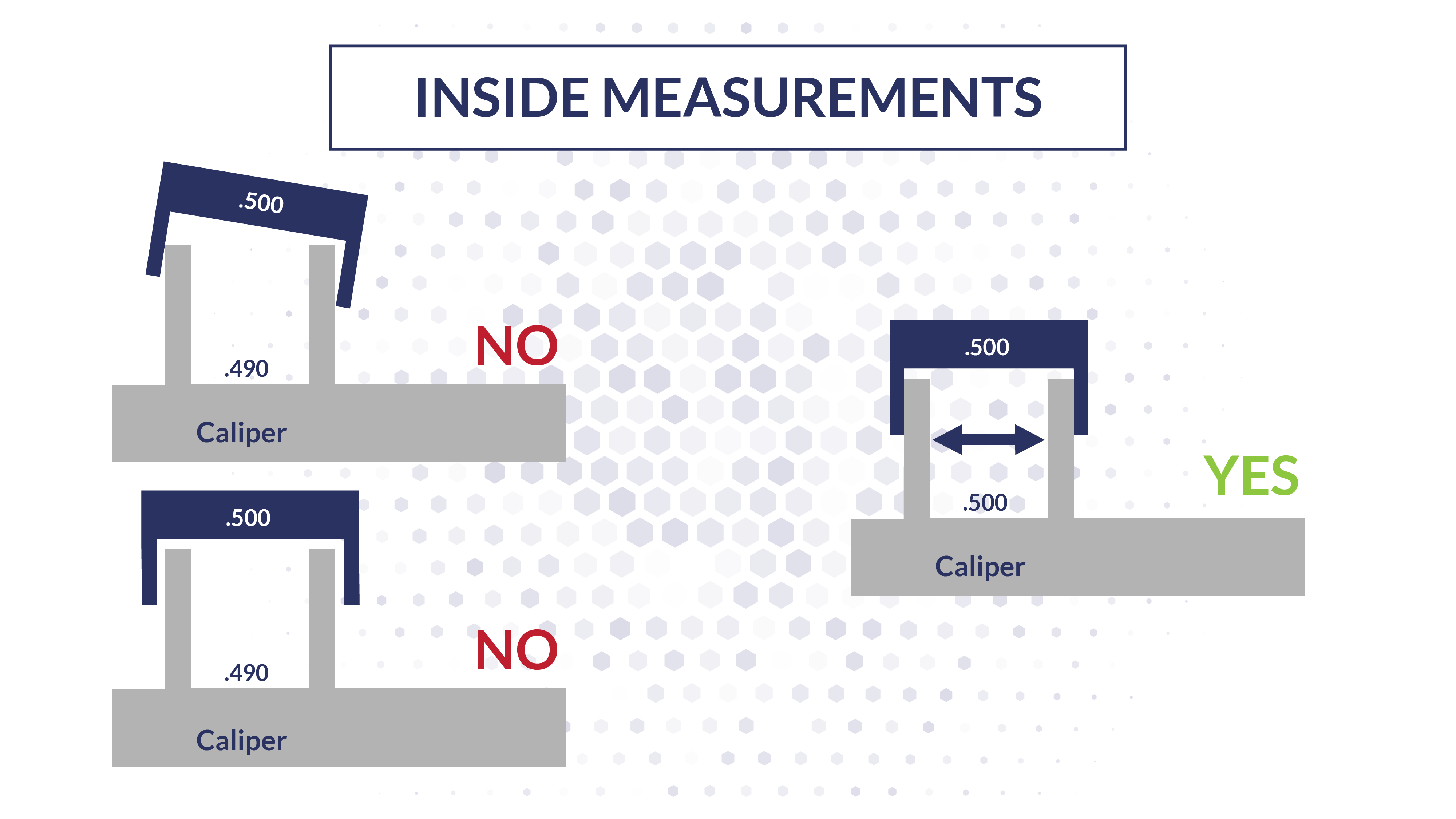
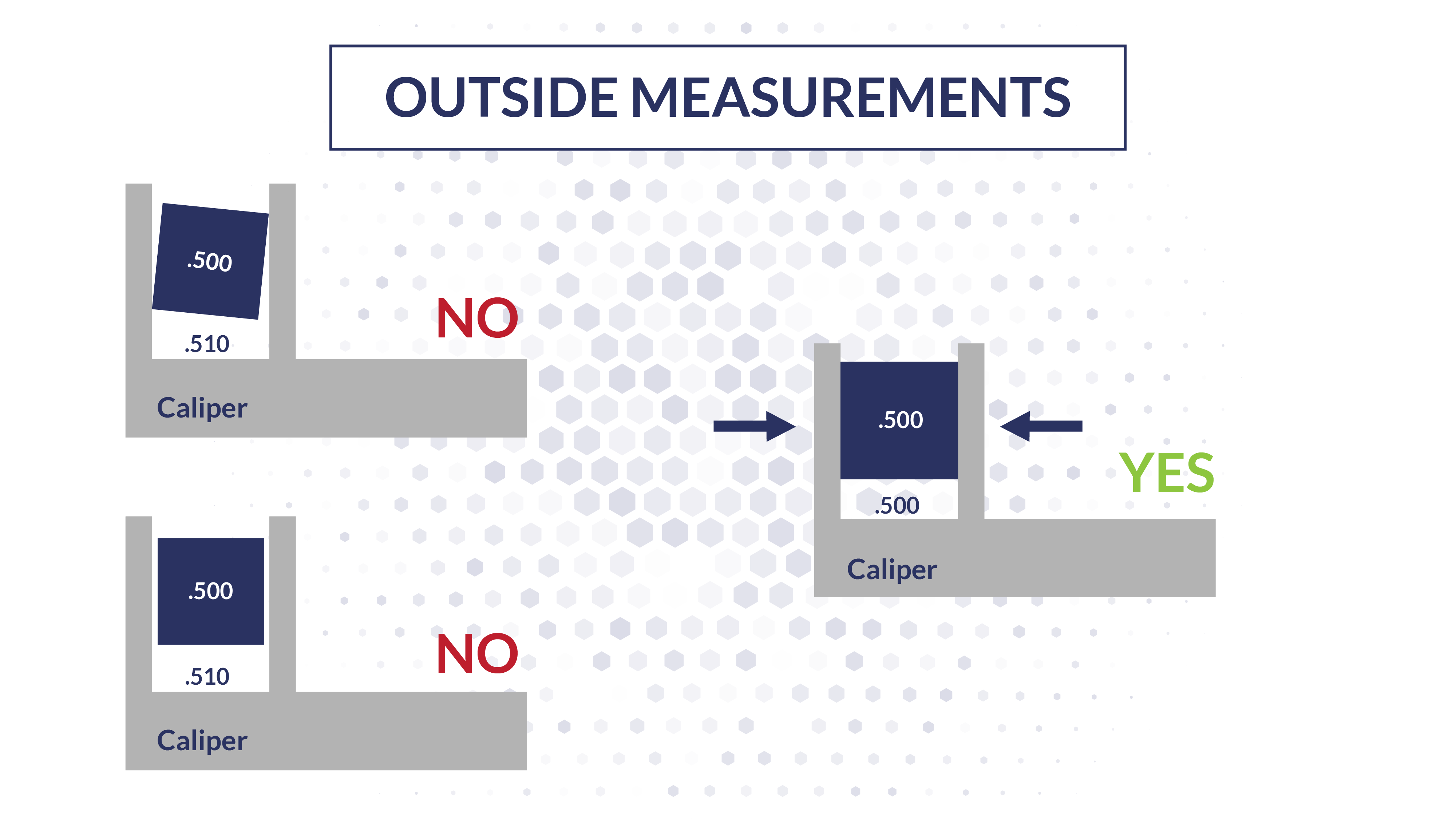
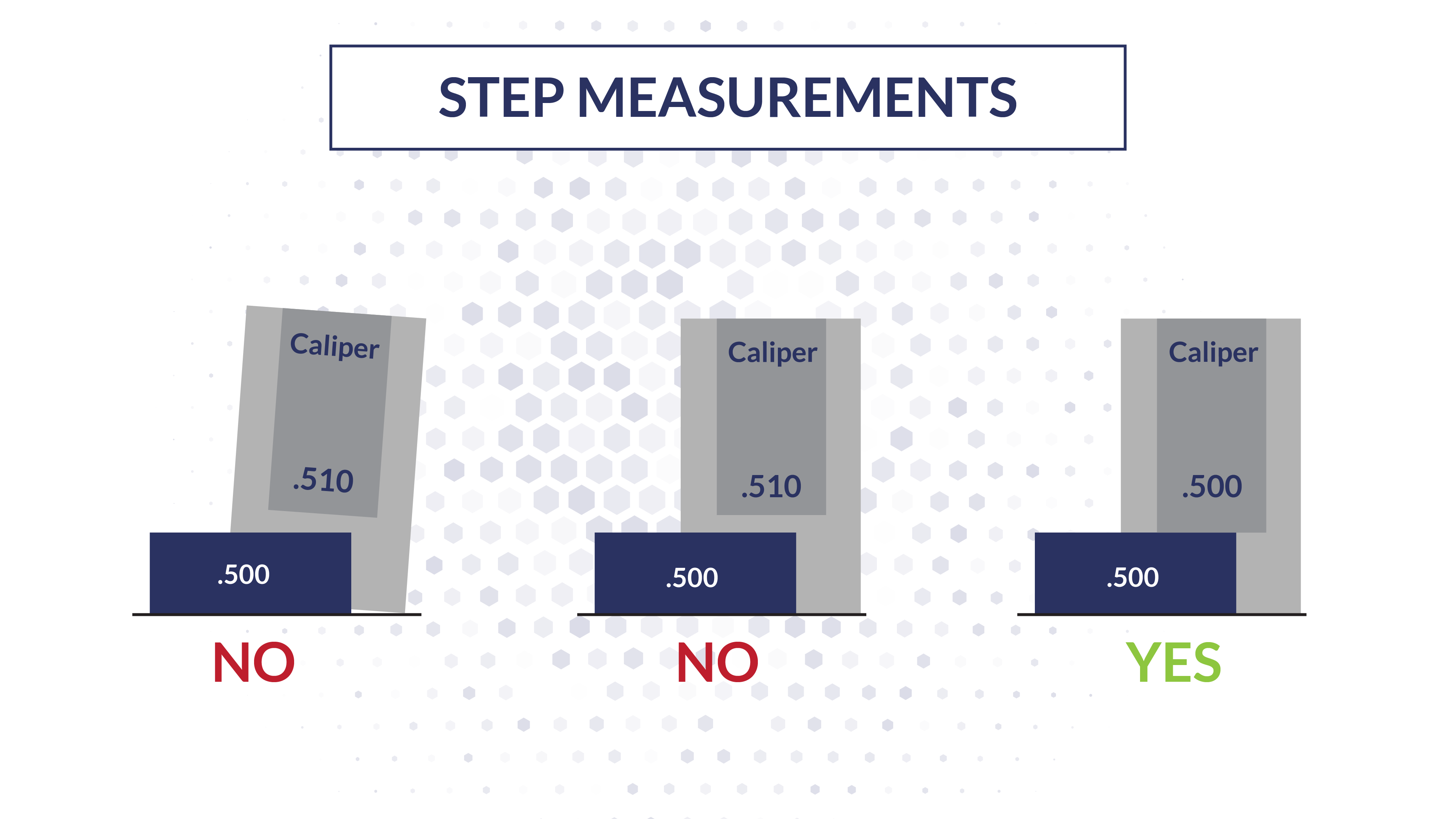
Calipers: Precision at Your Fingertips
Once you’ve understood the print, it’s time to bring it to life—and calipers are one of the most reliable tools to ensure accuracy. Whether measuring the outer diameter of a shaft, the depth of a recess, or the width of a slot, calipers deliver precise measurements across a range of applications.
Best practices when using calipers include:
Clean Surfaces: Dirt or debris can throw off readings.
Proper Jaw Contact: Ensure full contact with the part to avoid gaps.
Consistent Pressure: Excessive force can distort both the part and the tool.
Zero Point Verification: Always check the zero point before use.
Regular maintenance, including calibration checks and careful storage, ensures that calipers remain a dependable ally on the shop floor.
Thread Gauges: The Unsung Heroes of Fit and Function
While calipers handle dimensional accuracy, thread gauges ensure that threaded components meet both form and function requirements. Whether you’re working with screws, bolts, or tapped holes, thread gauges check that threads are cut correctly, fit properly, and comply with specified standards like NPT or NPT(F).
A few tips for using thread gauges effectively:
Visual and Tactile Checks: Look for burrs or defects that might interfere with assembly.
Confirm Fit: Ensure that male and female threads engage smoothly.
Check for Concentricity: Misaligned threads can compromise performance and lead to failure.
Incorporating thread gauge inspections into your workflow strengthens quality control, reduces assembly issues, and enhances end-product reliability.
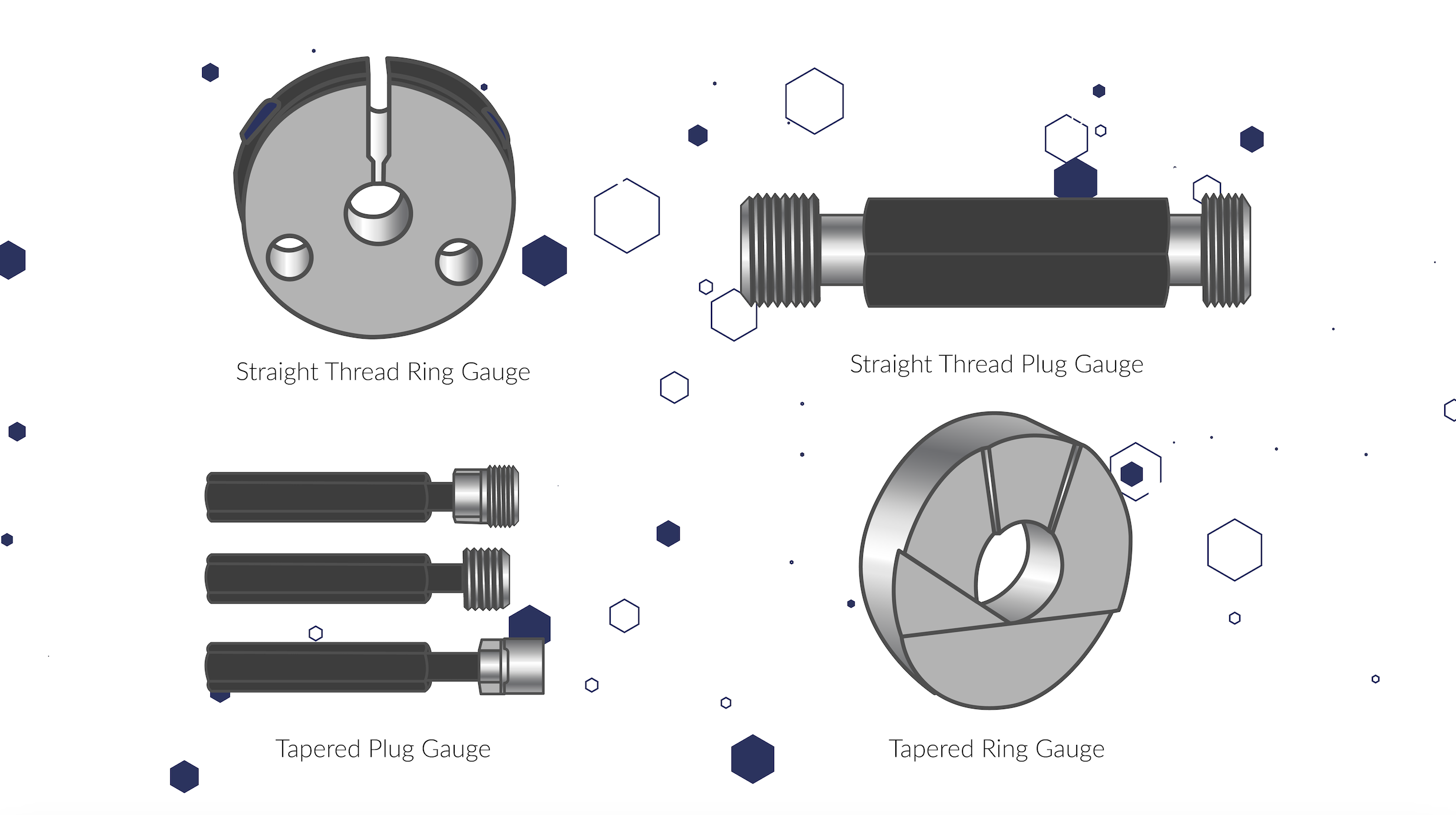
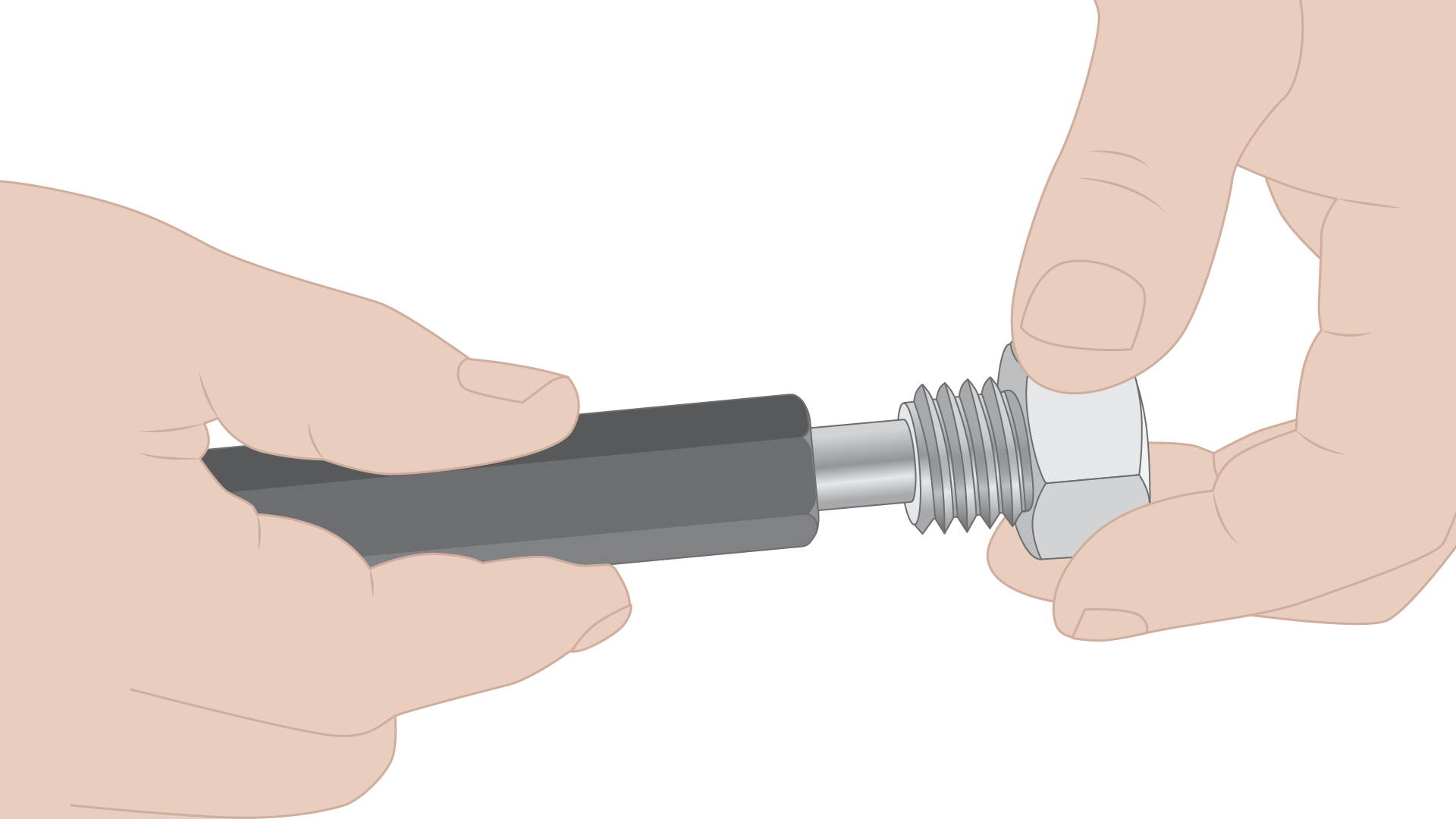
The Power of Integration
True manufacturing excellence comes from integrating these tools and skills. By combining sharp print comprehension with precise caliper measurements and thorough thread inspections, manufacturers create a quality-driven culture that consistently delivers superior results.
At Midland Industries, we champion these best practices to help our customers succeed. Whether you’re a seasoned machinist or just starting out, investing in these foundational skills and tools will pay dividends in performance, reputation, and customer trust.
Final Takeaway: Precision isn’t just a goal—it’s a mindset. By mastering technical prints, using calipers effectively, and relying on thread gauges for verification, you build a rock-solid foundation for manufacturing success.